Geschlossene Kühlkreisläufe
Grundsätzlich unterscheidet man zwei verschiedene Typen von Kreislaufkühlungen:
- Grundsätzlich unterscheidet man zwei verschiedene Typen von Kreislaufkühlungen:
- • geschlossene Kühlkreisläufe
Der wesentliche Unterschied ist, dass bei offenen Kühlkreisläufen (per Definition) allein die Verdunstungswärme des zirkulierenden Wassers zum Abkühlen genutzt wird. Dagegen werden solche Kühlkreisläufe als „geschlossen“ bezeichnet, die die Kühlwirkung nicht aus der Verdunstung beziehen, sondern entweder mit Luft oder mit einem sekundären Kühlsystem rückgekühlt werden, d.h. es wird kein Wasser (oder anderes Kühlmedium) aus dem geschlossenen Kreislauf zum Zwecke der Kühlung verdunstet. Bei Kühlkreistemperaturen über 5°C wird nahezu ausschließlich Wasser als Kühlmittel gewählt, welches hier, im Gegensatz zum offenen System, seine Qualität und Quantität während des Betriebes nur geringfügig ändert.
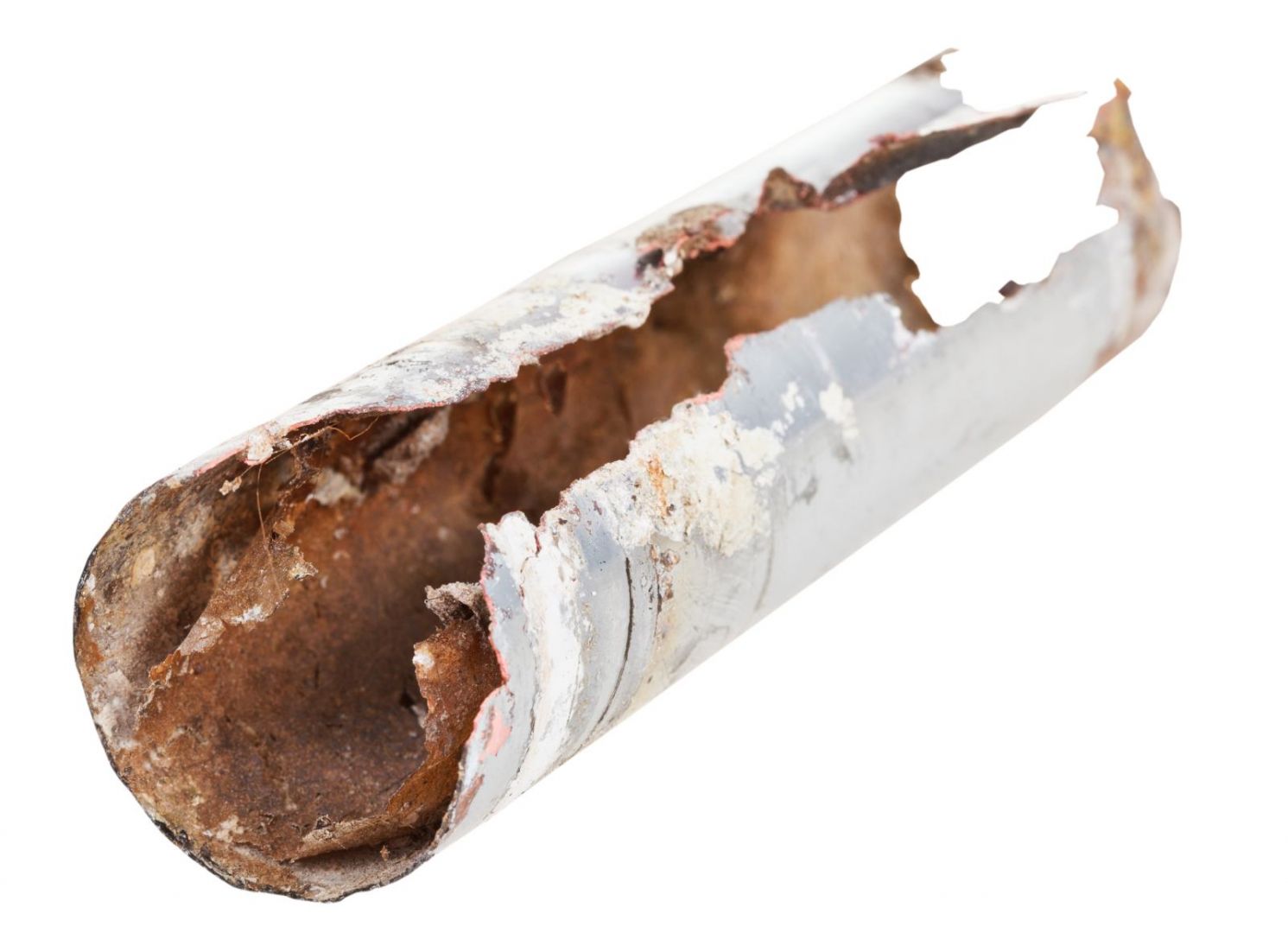
Für die Definition eines geschlossenen Kühlkreislaufs ist dabei unerheblich, dass es Prozess technisch häufig nicht zu vermeiden ist, dass das Kreislaufwasser mit der Atmosphäre oder dem Produktionsgut in Kontakt kommt, d.h. das geschlossene Kühlsystem ist in diesem Sinne meist nicht geschlossen. Die Folge ist, dass Verunreinigungen verschiedenster Art fortlaufend in das Wasser gelangen. Aber auch Wasserverluste sind die Regel, wie z.B. beim Werkzeugwechsel an Maschinen.
Geschlossene Kühlkreisläufe werden dann eingesetzt, wenn z.B. ein offener Kühlkreislauf konstruktionsbedingt die geforderte Kühltemperatur (< 18°C) nicht erreichen kann und eine Kältemaschine eingesetzt werden muss. Aber auch bei Kreislauftemperaturen über 30°C werden häufig geschlossene Kühlkreisläufe in Verbindung mit Trockenkühlungen (Luftkühler) und/oder zur Energieeinsparung Wärmerückgewinnungsanlagen eingesetzt. Dabei wird eine produktionsbedingte Prozesswärme zum Heizen anderer Anlagen genutzt.
Der große Vorteil eines geschlossenen Kühlkreislaufs ist, dass ein sehr hochwertiger Korrosionsschutz in diesem Kühlsystem zum bestmöglichen Schutz von wertvollen Maschinen eingesetzt wird und damit die geforderte Betriebssicherheit und Wirtschaftlichkeit gewährleisten kann.
In offenen Kühlkreisläufen lässt sich wegen des wesentlich rascheren Wasseraustausches nicht wirtschaftlich ein maximaler Korrosionsschutz erreichen. Das hier zur Kühlung verwendete (korrosive und/oder härteablagernde) Zusatzwasser gelangt nur in die robusten Rückkühlwerke und hat somit keinen direkten Kontakt mit den wertvollen Maschinen im primären Kühlkreislauf. Eine höhere Anlagensicherheit und ein verbesserter Werterhalt muss in diesem Fall den meist höheren Anschaffungskosten für dieses kombinierte Kühlsystem gegenübergestellt werden. Für ein Höchstmaß an Betriebssicherheit und Funktionalität der Produktion ist ein effizienter und reibungsloser Betrieb des gesamten Kühlsystems von großer Bedeutung.
Der Einsatz von Wasser als Kühlmittel in geschlossenen Kühlsystemen bringt aber in der Praxis in der Regel drei Probleme mit sich:
- Korrosive Wirkung des Wassers gegenüber Werkstoffen
- Belagsbildung und Korrosion durch Mikrobenwachstum
- Anorganische Ablagerung (Kalk,...) bei Wasserverlusten
Bedingt durch den unterschiedlichen Werkstoffeinsatz (Buntmetalle, Stahl,...) in den Kühlsystemen, durch die anlagenspezifischen Betriebsweisen (z.B. Temperatur, Anlagengröße,....) und nicht zuletzt durch die Wasserqualität in den Kühlsystemen ist es erforderlich, dass eine individuelle Wasserbehandlung durchgeführt werden sollte, damit ein sicherer und damit wirtschaftlicher Betrieb dauerhaft gewährleistet ist.
Gegenüber Eisenwerkstoffen hat unbehandeltes Wasser grundsätzlich eine korrosive Wirkung. Auch Buntmetalle (Messing, Kupfer,...) werden angegriffen, wenn Sauerstoff und Chloride zugegen sind. Und dies ist praktisch immer der Fall. Der fachgerechte, d.h. auch frühzeitige Einsatz von Korrosionsinhibitoren ermöglicht den Aufbau einer Schutzschicht auf den Materialoberflächen und reduziert damit den Angriff des Wassers.
Wegen der meist günstigen Lebensbedingungen (Temperatur, Nährstoffangebot) vermehren sich Bakterien (gelegentlich auch Algen) zum Teil sehr rasch. Gefördert wird das Wachstum von aeroben Mikroben dadurch, dass systembedingt das Kühlwasser mit der Atmosphäre und/oder mit dem zu kühlenden Produkt in Kontakt kommt.
Aber auch unter Sauerstoffausschluß können anaerobe Mikroben in den Belägen Stoffwechselprodukte bilden, die die Oberfläche korrodieren, wenn keine präventiven Maßnahmen ergriffen werden. Zusätzlich sind Systemstörungen, wie verschlechterter Wärmeübergang, mangelnde Hygiene, insbesondere wenn Mitarbeiter mit dem Kühlwasser in Berührung kommen, die Folge. Nur eine konsequente Qualitätsüberwachung des Kühlwassers und wirksame Desinfektionsmaßnahmen können hier zur angestrebten Anlagensicherheit führen.
Da geschlossene Kühlkreisläufe meist nicht gegen die Atmosphäre geschlossen sind, ist die Belagbildung durch ausfallenden Kalk dennoch ein kritischer Punkt in geschlossenen Kühlkreisläufen, wenn gelöste Kohlensäure durch Temperatur-erhöhung ausgasen kann. Es besteht die Gefahr, dass der ausfallende Kalk sich bei den hohen Betriebstemperaturen schnell auf den Wärmetauscheroberflächen abscheidet und den Wirkungsgrad verschlechtert. Vermieden werden kann dies entweder durch eine (Teil-) Enthärtung des Wassers und/oder durch Zusatz von Härtestabilisatoren.
Entscheidende Nachteile für den Betrieb von Kühlanlagen entstehen dadurch, dass durch die Belagsbildung an den Wärmetauscheroberflächen sich der Wärmeübergang verschlechtert, da die organischen (Schleim) und anorganischen Ablagerungen (z.B. Kalk) wie Isolatoren wirken.
Belagsbildung erhöht den Energiebedarf drastisch
Versuche haben gezeigt, dass schon bei einem 0,1 mm dicken Schleimbelag der Wärmeübergang um ca. 5–8 % verschlechtert wird. Bei 1 mm Schleimbelagdicke fällt der Wirkungsgrad um ca. 20 – 25 % ab. Vergleichbare Leistungsabfälle entstehen durch Kalkablagerungen an den Wärmetauscheroberflächen. In diesen Fällen muss der Kühlwasserstrom vergrößert werden, damit die gleiche Wärmemenge abgeführt wird. Dies erfordert eine deutlich größere Pumpenleistung. Ein erhöhter Stromverbrauch ist die Folge.
Ein weiterer Störfaktor entsteht durch das Ablösen von Ablagerungen jeder Art, wenn sich diese als kleinere oder größere Feststoffteilchen im Kühlsystem in Umlauf geraten. Rohrverstopfungen und Schäden an schnell laufenden Anlageteilen, wie z.B. in Umwälzpumpen, sind eine häufige Ursachen für unerwartete Funktionsstörungen, gleichbedeutend häufig mit Produktionsausfällen, wenn die Wärme an den Maschinen nicht ausreichend abgeführt wird. Sind Verkalkungen noch relativ leicht -sogar ohne den Betrieb zu unterbrechen- zu beseitigen, sind Bakterienschleimbeläge meist nur mit großem Reinigungsaufwand zu entfernen und sollten daher dringend vermieden werden.
Für eine Optimierung der Wärmeübergänge an den Wärmeaustauscherflächen und für einen energiesparenden Betrieb ist eine konsequente Wasserbehandlung in den geschlossenen Kühlkreisläufen ebenso unerlässlich wie die Wartung der primären Produktionsanlagen.
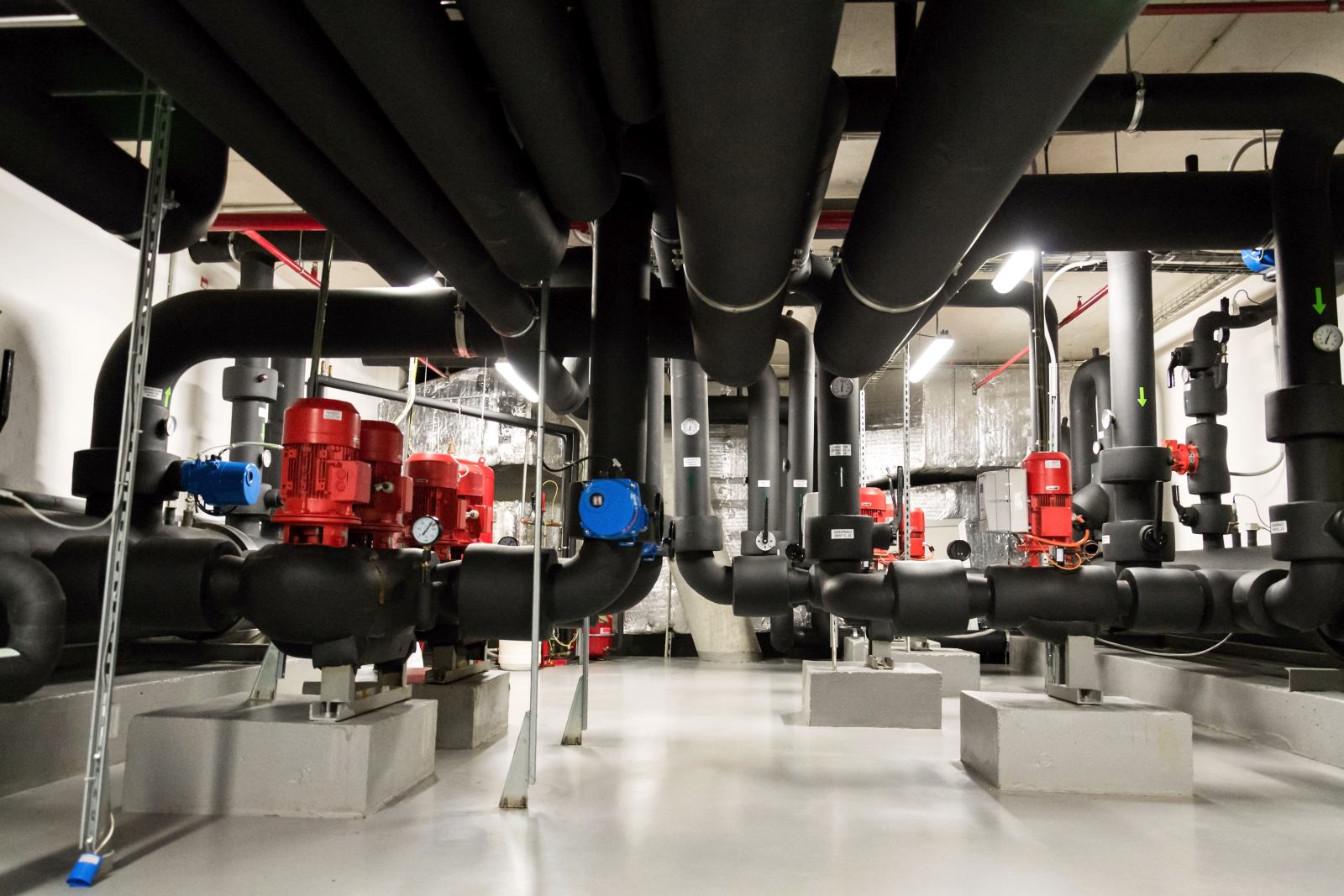
Ihre Vorteile einer konsequenten Wasserpflege in geschlossenen Kühlsystemen sind:
- Korrosionsschutz durch Ausbildung einer Schutzschicht auf den Materialoberflächen
- Schutz vor Belagsbildung durch Härtestabilisierung
- Verbesserte Hygiene durch effektive und kontrollierte Mikrobenbekämpfung
Das bedeutet:
- Verbesserte Werterhaltung der Anlage durch Korrosionsschutz
- Verbesserte Werterhaltung der Anlage durch Korrosionsschutz
- Erhöhte Betriebssicherheit
- Kostenersparnis
Iceco und Aqua-Concept haben durch eine lange Erfahrung im Bereich der technischen Wasserbehandlung spezielle Pflegeverfahren für geschlossene Kühlsysteme entwickelt, die seit vielen Jahren erfolgreich von zufriedenen Kunden eingesetzt werden.
Die in diesem Pflegeprogramm eingesetzten Produkte zeichnen sich durch die folgenden Eigenschaften aus:
- Keine Geruchsbelästigung, da Verzicht auf chlorhaltige Wirkstoffe
- Automatische Dosierung für alle Produkte möglich
- Verhindern von Resistenzen durch Wirkstoffdifferenzierung
- Variable Dosiertechnik kann jedem System angepasst werden
- Bedienerfreundliche und zeitsparende Behandlungssysteme
- Frostschutzmittel kombiniert mit Korrosionsinihibitoren
Die besonderen Vorteile dieser Verfahren sind:
- Effektive und dennoch umweltfreundliche Wirkstoffe und Wirkstoffkombinationen
- Systematische Überwachung der Anlagen durch Analytik, Dosier- und Absalzkontrolle sowie Bestimmung von Korrosionsraten
- Fachkundige Außendienstspezialisten beraten und unterstützen prompt. Natürlich auch vor Ort
Beispiel eines Pflegeprogramms für geschlossene Kühlsysteme
Ein mögliches Pflegekonzept mit für geschlossene Kühlkreisläufe kann in vier Schritte gegliedert werden (in Kurzfassung):
Schritt 1: Grundreinigung (wenn möglich)
Bei Bedarf zum Entfernen von Belägen Decalcit T 131 (Kalk) oder Decalcit T 610 (Rost und Kalk) in das mit Wasser gefüllte Kühlsystem einbringen und bei guter Entlüftung (CO2-Entwickung) das Wasser umwälzen. Danach den Kreislauf mehrmals gut spülen.
Schritt 2: Inbetriebnahme des geschlossenen Kühlsystems
Befüllen des Kühlkreislaufes, falls erforderlich mit aufbereitetem Wasser. Gleichzeitig mengenproportionale Zugabe von CORAGARD Inhibitor (Korrosionsschutz; ca. 3000 g pro m³ Systemwasser) und von geeignetem Biozid (ca. 100 g pro m³ Systemwasser) je nach Wasserqualität.
Schritt 3: Dauerbetrieb
Die Dosierung von CORAGARD Inhibitor zum Zusatzwasser sollte mengenproportional über einen Kontaktwasserzähler erfolgen. Die Zugabe von Biozid sollte je nach Keimbelastung per Hand, über Zeitschaltuhr oder über die Absalz- und Dosiersteuerung in regelmäßigen Abständen erfolgen. Zur Kontrolle der Keimbelastung im Systemwasser eignen sich spezifische Nährboden-Träger (Zubehör: Easicult-Combi Dip-slides Art. nr D3500100) sehr gut.
Schritt 4: Wasserwechsel
Je nach Betriebsdauer und Systembeanspruchung sollte im Abstand von ca. einem Jahr das Systemwasser ausgetauscht werden. Insbesondere wenn sich durch die Produktion organische und anorganische Stoffe im den Wasserkreislauf ansammeln, sollte eine Reinigung wie in Schritt 1 beschrieben wiederholt werden.